智化控优——化工流程智能控制与优化系统
开发者:汪子奇 陈诺
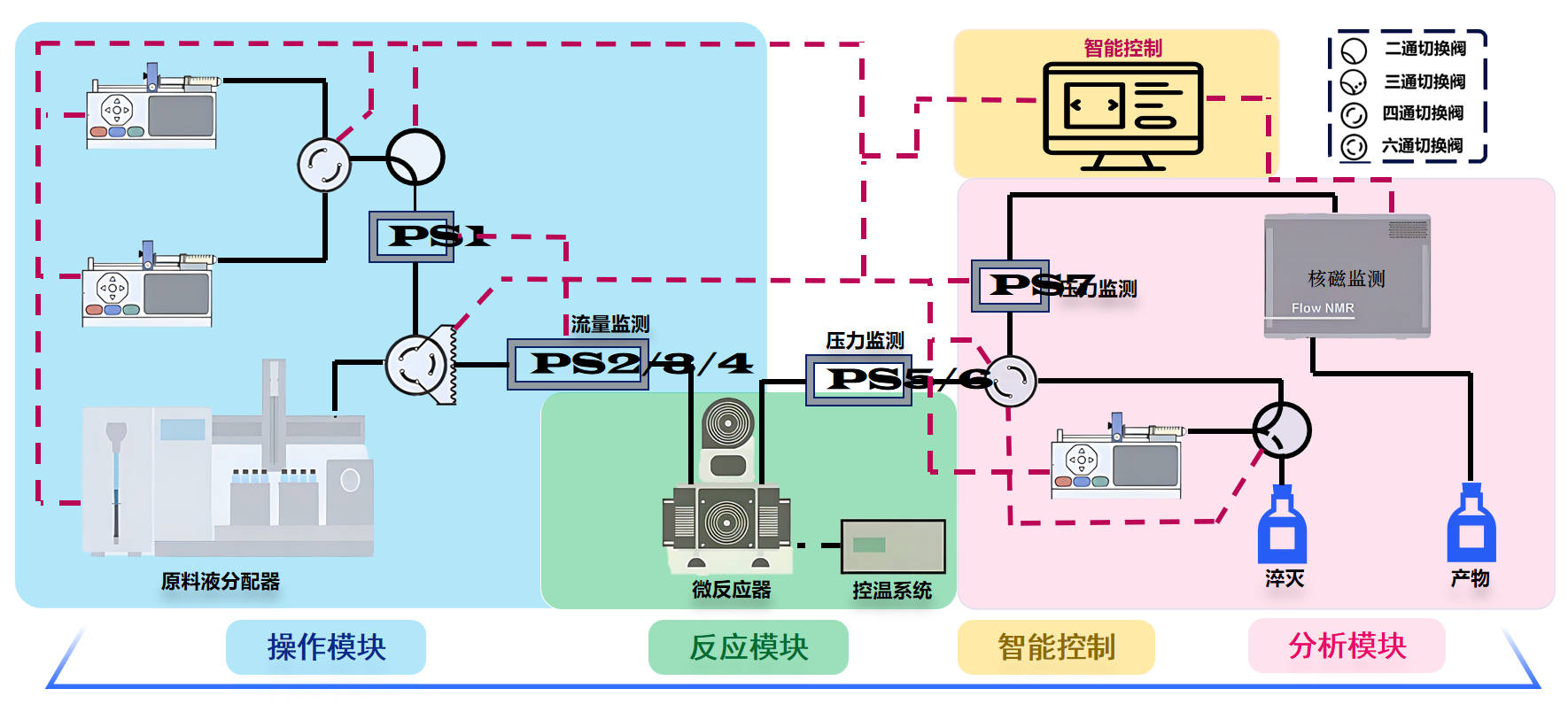
为了推动制造业数字化转型,助力新型工业化的发展,构建现代化产业体系,设计并开发了一个微纳连续制造智能控制系统平台。该平台旨在优化制造流程管理、设备控制、过程监控、数据分析以及智能提升。通过 AI 智能体开发与嵌入、AI 模型协同训练、设备接入和任务调度的智能规划,实现制造过程的实时监控、异常告警与根因定位等功能,最终实现制造全过程的智能化与云端协同控制。该研究实现了制造设备的统一管理,降低了软件开发的复杂性,提高了控制参数的灵活性和响应速度,简化了生产线的维护和拓展,并有效应对生产问题的动态变化。
复杂流程难以控制:化工制造流程通常涉及多个复杂设备和工艺参数,传统方法难以实现高效管理和精确控制。通过智能控制与优化系统,平台实现了多设备、多流程的统一管理和动态调度,降低了操作复杂性。
实时监控与异常处理不足:传统生产线难以实现实时过程监控与异常问题的快速响应。该系统通过嵌入AI模型协同训练和智能任务规划,实现了制造过程实时监控、精准异常告警及根因定位,确保生产稳定性和安全性。
柔性生产需求应对不足:生产需求的动态变化对制造流程的柔性和扩展性提出了更高要求。该平台通过灵活的控制参数调整与云端协同,实现了快速响应生产需求变化并简化生产线维护和扩展。
数据利用率低:制造过程中的数据未能充分挖掘其价值。通过数据分析和智能提升,平台将实时数据转化为优化控制策略,提高生产效率和资源利用率。
智能化与协同控制:集成AI智能体开发、AI模型协同训练和智能任务规划,实现生产全过程的智能化管理与云端协同控制,大幅提升流程效率与智能化水平。
实时监控与异常处理:平台支持对制造流程的实时监控,能够进行精准异常告警与快速根因定位,减少因故障导致的停机时间,保障生产的连续性与安全性。
灵活的设备接入与参数控制:支持多种制造设备的无缝接入,优化控制参数的灵活性和调整速度,适应生产流程的动态变化,提升了系统的适应性与扩展能力。
高效的数据分析与优化:利用数据驱动的AI分析技术,将制造数据转化为优化建议与控制策略,实现持续优化的制造流程和资源分配。
简化的系统维护与拓展:系统通过统一管理制造设备,降低软件开发复杂性,简化生产线的维护和扩展,实现灵活生产和快速部署能力。